Generally, there are three types of tyre pyrolysis plants, batch operating plants, semi-automatic operating plant and fully continuous operating plant. However, the two operating systems are still many differences.
Model | BLJ-6 | BLJ-10 | |
Daily Capacity | 6T | 8-10T | |
Working Method | Batch | ||
Raw Materials | Waste Plastic, Tyre, Rubber, Oil Sludge | ||
Reactor Size | D2.2*L6.0m | D2.6*L6.6m | |
Pattern | Rotary | ||
Heating Materials | Charcoal, Wood, Fuel Oil, Natural Gas, LPG, etc. | ||
Total Power | 24kw/h | 30kw/h | |
Floor Area (L*W*H) | 30*10*8m | 30*10*8m | |
Service Life | 5-8 Years |
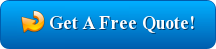
Model | BLJ-16 |
Daily Capacity | 15-20T |
Working Method | Semi-Continuous |
Raw Materials | Waste Plastic, Tyre, Rubber, Oil Sludge |
Reactor Size | D2.8*L7.1m |
Pattern | Rotary |
Heating Materials | Charcoal, Wood, Fuel Oil, Natural Gas, LPG, etc. |
Total Power | 54kw/h |
Floor Area (L*W*H) | 40*10*8m |
Service Life | 5-8 Years |
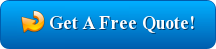
Model | BLL-20 |
Daily Capacity | 20-24 T |
Working Method | Fully Continuous |
Raw Materials | Waste Plastic, Tyre, Rubber, Oil Sludge |
Reactor Size | D1.4*L11 m |
Pattern | Horizontal |
Heating Materials | Charcoal, Wood, Fuel Oil, Natural Gas, LPG, etc. |
Total Power | 71.4kw/h |
Floor Area (L*W*H) | 45*25*10m |
Service Life | 5-8 Years |
Waste Tyre Pyrolysis Process
1.Pretreatment
For the continuous type, its feeding hole is very small, so it needs a shredder machine to cut tyre into small pieces (about 30-50mm). While for the batch system, the tyre can be directly put into the reactor without being pretreated.
2. Feed raw materials
For the continuous type, the waste tires can be put into reactor by an auto-feeder. While for the batch type, this process is manual.
Heat the reactor using fuel materials, such as coal, charcoal, fuel gas, wood etc. The reactor will be slowly heated, when the temperature reaches around 250℃, the oil gas will be produced.
4. Condensing
A part of oil gas will be processed by our technology and then goes to cooling system to form liquid oil. We adopt new-type condenser which can improve the oil yield efficiency and make the oil yield to the maximum.
5. Extra gas recycling
The gas which cannot be liquefied under normal pressure will go back to combustion system. It can be used as fuel material to heat the reactor, which will save energy for the whole working process.
6. Discharge
In the process, there are also carbon black and steel wire produced. For the continuous type, the discharging of these two products are both automatic. While for the batch type, the discharging of steel wire is manual. When the temperature falls down to 40℃, workers can open the door and take the steel wire out.
When the whole working process has been finished, the reactor of the batch type must be cooled and then you can start another batch. After knowing their different working processes, you can choose the plant and system according to your actual need. For more requirement, we can also provide you with customized plants.
Basic Parameter:
Model | BLJ-6 | BLJ-10 | BLJ-16 | BLL-20 |
Daily Capacity | 6T | 8-10T | 15-20T | 20-24T |
Working Method | Batch | Semi-Continuous | Fully Continuous | |
Raw Materials | Waste Plastic, Tyre, Rubber, Oil Sludge | |||
Reactor Size | D2.2*L6.0m | D2.6*L6.6m | D2.8*L7.1m | D1.4*L11m |
Pattern | Horizontal & Rotary | |||
Heating Materials | Charcoal, Wood, Fuel Oil, Natural Gas, LPG, etc. | |||
Total Power | 24kw/h | 30kw/h | 54kw/h | 71.4kw/h |
Floor Area (L*W*H) | 30*10*8m | 30*10*8m | 40*10*8m | 45*25*10m |
Operating Pressure | Normal Pressure | Constant Pressure | ||
Cooling Method | Water Cooling | |||
Service Life | 5-8 Years |