1. Brief introduction of automatic continuous waste tyre pyrolysis plant
If time goes back to 3-5 years ago, batching tire pyrolysis machines were the most popular products. But this kind of machine mainly depends on labor to operate, and the whole process not only wastes time but consumes energy. With the faster development of pyrolysis plant business, more and more people want to pursue the higher and faster economic efficiency. Thus we have developed the fully continuous waste tyre pyrolysis plant to meet this demand. However, there is no doubt that this machine is also based on the batching plant, so their major pyrolysis processes are consistent. The latter is merely more intelligent and more convenient on operation, which also reduces more manpower and material resources. Compared with the small scale pyrolysis machines, the major advantage of the automatic continuous waste pyrolysis plant is that it can work continuously; both automatic feeding and discharging will save a lot of time without cooling before discharging to make the whole pyrolysis process more efficiency.
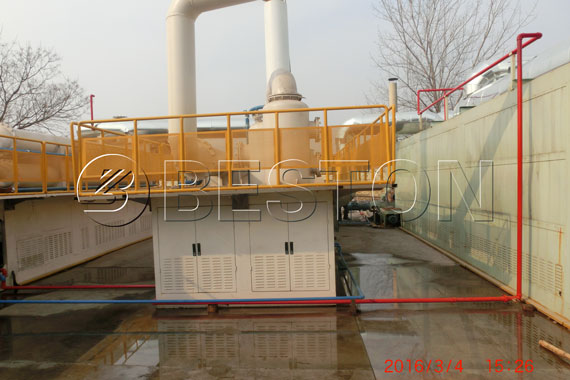
2. Operation flow of fully continuous waste tyre pyrolysis machine
Pretreatment device of waste tires
Different from small pyrolysis machine, in order to ensure that the raw material can be fed continuously in a sealed and uniform feeding system, the continuous pyrolysis plant must have a tire shredder pretreatment. The size required blow 3-5 cm is better.
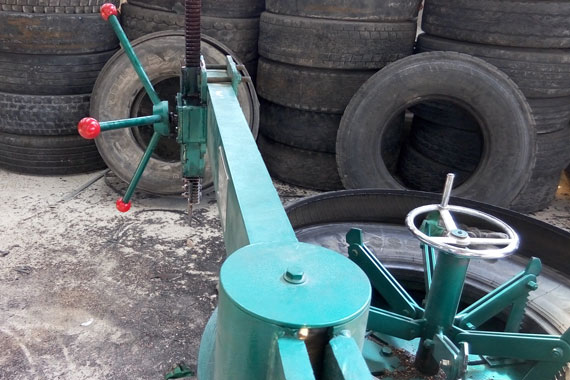
Feeding
Our automatic pyrolysis plant adopts screw sealed conveyor to feed, and the feeding machine can set feeding speed to control the whole process in order. What’s more, the feeding machine equips the air blower which can ensure that there is no air in the pyrolysis reactor to efficiently avoid the security implications.
Heating and pyrolysis
The fully continuous tyre pyrolysis plant has introduced the indirectly heating system, so the flame will not contact the intine of the reactor directly. Heating source contacts the pyrolysis system through the burner, heating by hot air or its conduction. In this way, it can extend the life time of the reactor and heat uniformly.
Cooling
As the batching pyrolysis plant, cooling system is also an important part of the waste pyrolysis system. The good cooling system can cool the oil gas produced by pyrolysis of tires thoroughly to increase the oil yield.
Discharging
Continuous pyrolysis equipment uses the screw conveyor to connect the most terminal of the reactor to flush off. Besides, the outside of the screw conveyor has recycling cooling layer which can prevent the effluent carbon black from overheating to destroy the discharging equipment and scalding workers.
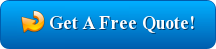
3. Finished products of pyrolysis plant:
Pyrolystic oil
a. The tire pyrolysis oil can be used as fuel oil in industry or heating furnace, such as cement plant, steel plant, glass factory and so on.
b. Refined to diesel to be used in diesel fuel and power plant, agricultural machinery.
Carbon black
a. Can be compressed into ball for industry heating, and the calorific value is equal to the coal, which can be replaced directly.
b. Can be refined into power of different standards, used as additive in paint, rubber.
Steel wire
a. Sell it to the waste recycling station.
b. Sell it to the iron and steel plant, to be smelted again.
4. Advantages of the automatic continuous tire pyrolysis machines
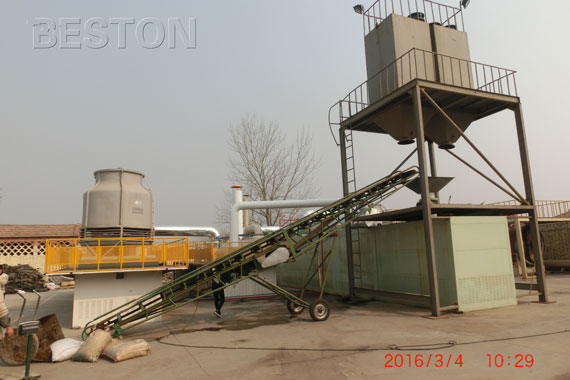
High efficiency, large capacity
The machine can work continuously 24 hours a day, with high efficiency and large output. Through the design of multiple reactor, the maximum output can reach 24 tons per day.
PLC intelligent operation
Our machines introduce PLC or computer intelligent control to reduce the manpower and cost, and also make the process more convenient and faster.
Design of multiple reactor
The machine uses the unique multiple pyrolysis reactor design, and we can design different reactors according to the client’s demand.
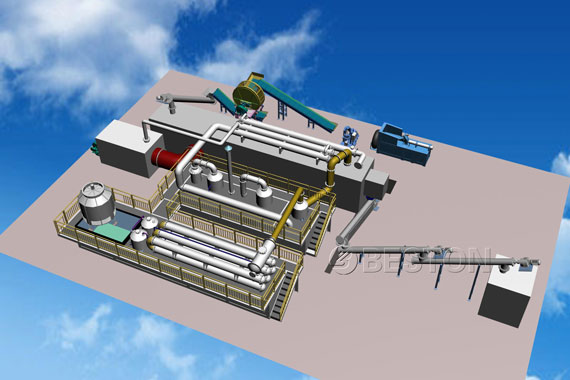
Indirect and uniform heating
The continuous waste tyre pyrolysis plant designed by Beston Machinery adopts the indirect heating by hot wind and air, and the heating source does not get in touch with the reactor, which can prolong the reactor’s service life and ensure heating uniformly and efficiently.
Internal rotation transmission system
We all know that the old pyrolysis reactor needs to rotate continuously and keep uniform heating in order to ease feeding and discharging, but the reactor rotating standing for the reactor and the connection of tubular are sealed to prevent the security implication because of the air leaking of the reactor. However, the sealed material is not permanent and durable, and generally, it needs to stop the machine to change the seal materials in 1-2 days. If in this method, it is out of the question to realize the continuous working. So we have introduced the internal rotation delivery system which does not need to use the sealed materials and even does not need to stop machine to change the materials. Thus it can fully realize the continuous operation.
Basic Parameter:
Model | BLL-20 |
Daily Capacity | 20-24 T |
Working Method | Fully Continuous |
Raw Materials | Waste Plastic, Tyre, Rubber, Oil Sludge |
Reactor Size | D1.4*L11 m |
Pattern | Horizontal |
Heating Materials | Charcoal, Wood, Fuel Oil, Natural Gas, LPG, etc. |
Total Power | 71.4kw/h |
Floor Area (L*W*H) | 45*25*10m |
Operating Pressure | Constant Pressure |
Cooling Method | Water Cooling |
Service Life | 5-8 Years |